بلوک فولادی Mo40
بلوک فولادی Mo40 از دسته فولادهای آلیاژی عملیات حرارتی پذیر بوده که در استاندارد DIN آلمان به نام فولاد ۱.۷۲۲۵ معروف و در بازار ارائه می شود. دمای فورجینگ mo40 در حدود 1050-850 درجه سانتیگراد می باشد. دو عنصر کروم و مولیبدن در این فولاد باعث افزایش چقرمگی آن می شود. فولاد 7225 تا دمای 932 درجه سانتیگراد کار می کند. میزان کروم موجود در این فولاد باعث افزایش مقاومت به حرارت در آن می شود.
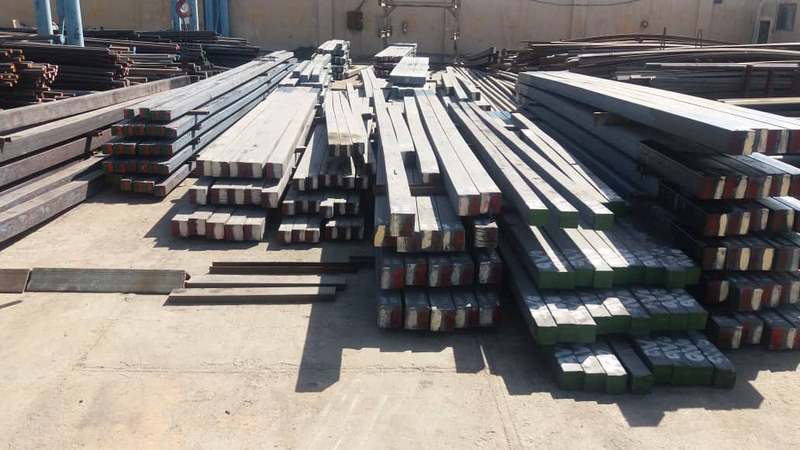
مشخصات فولاد Mo40 ( بلوک فولادی Mo40 )
فولاد Mo40 ( بلوک فولادی Mo40 ) در درجه 860 – 900 درجه سانتی گراد حرارت دیده می شود و باید حرارت به طور یکسان به تمام نقاط میلگرد انتقال پیدا کند. بعد از آن به مدت 20 دقیقه در آب و پس از آن در هوا خنک می شود. دمای آنیل میلگرد Mo40 بین 800 – 850 درجه سانتی گراد است که مطابق بالا باید به طور یکسان حرارت دیده شود و سپس در آب خنک می شود. دمای برگشت (Tempering) میلگرد mo40 بین 550 – 700 درجه است و سایر مراحل نیز مطابق مراحل بالا انجام می شود.
این فولاد بیشتر برای تولید قطعات صنعتی مانند چرخ های جرثقیل که در معرض ساییدگی هستند استفاده می شود. اما در شرایط کار ، مقاومت آنها دربرابر سایش پس از مدتی به دلیل سختی کم آن کاهش می یابد. با افزایش ساییدگی، سایز قطعات کاهش یافته و برای اصلاح سطح نیاز به تعمیر دارند. به همین جهت، برای استفاده مجدد از این آلیاژها، از روکشهای سفت با فرآیند روکش کاری سخت (hard-facing) استفاده می شود.
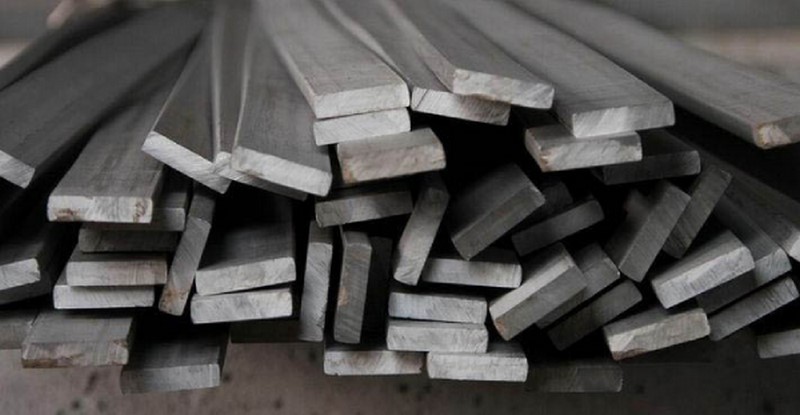
اثر عناصر آلیاژی بر روی خواص فولاد Mo40
– عنصر کروم
وجود این عنصر در فولادهای Mo40 و فولاد Ck45 باعث افزایش قابلیت سختی پذیری و پایداری فولادها در درجه حرارت های بالا می شود. که کاربرد فولادهای کروم دار را در ساخت قطعات مقاوم به حرارت و گرم کار افزایش می دهد. بلوک فولادی Mo40
استفاده از کروم در مقادیر بالا باعث بهبود مقاومت به خوردگی و اکسایش میشود. استحکام فولادهای کروم دار بالاست ولی مقاومت به ضربه، انعطاف پذیری و خواص جوشکاری آن ها تا حدودی پایین است. کروم سختی فولاد Mo40 و مقاومت به سایش را با تشکیل کاربید به واسطه حضور کربن افزایش میدهد. استحکام کششی و تسلیم فولادها با افزایش کروم، موجب کاربرد وسیع آنها در ساخت قطعات صنعتی می شود.
– عنصر سیلیسیم
اکثرا در آهن خام مقادیری سیلیسیم یافت می شود و در برخی مواقع از جداره های نسوز کوره در عملیات ذوب جذب مذاب می گردد.
به همین دلیل سیلیسیم در تمامی انواع فولادها حضور دارد، این عنصر یکی از عناصر اکسیژن زدا در فولادها می باشد. برای افزودن سیلیسیم به مذاب معمولا از آمیژان استفاده می شود.
سیلیسیم در فولادها اعم از Mo40 مقاومت به پوسته شدن در درجه حرارت های بالا را افزایش می دهد. این عنصر مقاومت در برابر اکسید شدن را افزایش داده و موجب افزایش مقاومت فولادها می شود که در صورت حضور آن تا چهارده درصد در ترکیب فولاد، قابلیت آهنگری فولاد به شدت کاهش می یابد. این عنصر در افزایش سختی پذیری فولادهای دارای عناصر گرافیت زا موثر است.
– عنصر مولیبدن
مولیبدن موجب بالا بردن سختی پذیری و عمق سختی فولادها می گردد. این عنصر در بهبود خواص جوشکاری فولادها موثر است با این حال در مقادیر زیاد موجب کاهش خواص آهنگری می شود. مولیبدن در دسته عناصر کاربیدزا قرار دارد و به دلیل تولید کاربیدهای پایدار، دمای درشت شدن دانه های آستنیت را افزایش داده و از رشد دانه ها جلوگیری می نماید و سبب ریز شدن دانه ها می شود که در نتیجه چقرمگی فولاد را افزایش می دهد.
این عنصر معمولا در کنار عناصر دیگر مثل نیکل و کروم استفاده می گردد که موجب بهبود برخی از خواص از جمله افزایش استحکام کششی و عمق سختی می شود و در فولادهای زنگ نزن موجب افزایش مقاومت به خوردگی می گردد. این عنصر همچنین موجب بالا رفتن استحکام کششی و خزش گرم و حفظ سختی در دمای بالا و مقاومت حرارتی فولادها می شود و با تردی حرارتی مقابله می نماید. از این عنصر در ساخت قطعات مقاوم به سایش نیز استفاده می شود.
– عنصر منگنز
این عنصر یکی از اصلی ترین عناصر در فولادها بوده و در اکثر آن ها یافت می شود. منگنز یک اکسیژن زدای موثر می باشد که سبب افزایش سختی پذیری و عمق سختی رمی گردد. این عنصر تردی و شکنندگی فولادها را در درجه حرارت های بالا که ناشی از اثر گوگرد است، کاهش می دهد. منگنز در بهبود کیفیت سطحی فولادها موثر است و افزایش آن به فولادها موجب درشت شدن دانه های فولاد می شود ولی حضور آن در مقادیر خیلی بالا موجب شکنندگی فولاد می شود.
وجود منگنز در فولادها در افزایش استحکام فولاد تاثیر زیادی داشته ولی بر خواص الاستیسیته تاثیر خیلی کمی دارد و در بهبود خواص جوشکاری و آهنگری موثر است. منگنز در حضور کربن موجب افزایش مقاومت به سایش می شود. مقدار زیاد این عنصر باعث پایداری آستنیت در دمای محیط می شود.
– عنصر فسفر
استفاده از فسفر در فولادها اثرات نامناسبی بر چقرمگی و انعطاف پذیری می گذارد و چنانچه مقدار آن به بیش از ۰.۲ درصد برسد استحکام ضربه ای به شدت کاهش می یابد.
میزان فسفر در فولادهای با کیفیت بالا، حداکثر ۰.۰۳ تا ۰.۰۵ درصد است. فسفر در شکنندگی و کاهش شکل پذیری فولادها تاثیر زیادی دارد که به واسطه افزایش کربن، تشدید می گردد و به صورت فسفد آهن در مرزدانه ها رسوب می کند و موجب سردشکنی و کاهش شکل پذیری و استحکام می شود. فسفر در فولادها علاوه بر اثرات مضر دارای فوایدی نیز می باشد. یکی از فواید آن افزایش استحکام در حالت محلول جامد می باشد.
– عنصر گوگرد
این عنصر در فولادها به عنوان یک ناخالص محسوب می شود. گوگرد موجب تثبیت و پایداری سمنتیت می شود. این عنصر با آهن تشکیل ترکیب یوتکتیکی FeS می دهد. حضور این ترکیب با نقطه ذوب پایین در مرزدانه ها موجب منفصل شدن دانه ها در حین عملیات حرارتی و نورد شده و در نتیجه منجر به ایجاد ترک گرم و تردی شکنندگی فولادها می شود.
به طور کلی گوگرد در فولادها به عنوان عنصری نامناسب معرفی می گردد ولی مقادیر کمی گوگرد در حدود ۰.۳ درصد در گروهی از فولادهای خوش تراش به جهت بهبود خواص تراشکاری و ماشین کاری مورد استفاده قرار می گیرد.

روش تولید بلوک فولادی MO40
مزید اطلاعتان از این موضوع که آلیاژ MO40 چیست باید بگوییم که این آلیاژ در دسته فولادهایی قرار می گیرد که در برابر حرارت مقاومت بالایی از خود نشان می دهند و در حقیقت دارای کیفیت بسیار خوبی هستند. این نوع فولاد با نام های MO40 و 4140 شناخته می شود. این فولادهای آلیاژی بر اساس استاندارد AISI ساخته می شوند و در ترکیب خود دارای عناصر کروم و نیکل هستند. گاهی اوقات به منظور حذف کروم از ترکیب MO40 از 0.2 درصد نیکل در آن استفاده می شود. دلیلش هم این است که وجود کروم در این فولاد آلیاژی باعث شکننده شدن آن میشود.بستلوک فولادی Mo40
چگالی فولاد MO40
وجود دو عنصر کروم و مولیبدن در فولاد MO40 موجب افزایش چقرمگی در این فولاد می گردد. فولاد MO40 برای ساخت تجهیزات صنعتی مانند تیر، ستون، چرخ دنده و غیره به کار میرود، این تجهیزات معمولا تحت فشار یا ضربه و حرارت بالا قرار دارند. بهتر است بدانید به دلیل سختی بسیار زیاد این فولاد، در پروژه هایی که مقاومت به سختی و توان کششی بالا مدنظر باشد مورد استفاده قرار می گیرد. کاربردهای متعدد این فولاد و تقاضای بسیاز زیاد آن در بازار فروش فولاد باعث شده است تا قیمت فولاد mo40 همواره در حال نوسان باشد.
كاربردها و موارد استفاده از فولادMO40 (بلوک فولادی MO40)
فولاد آلیاژی MO40 در صنایع مختلفی از قبیل غلتک سیمانی ، غلطک فلزی ، شفت ، چرخ دنده ، دوفصل ، محور ماشین ، چرخ دنده فرمان ، پیچ های پایدار ، میله اتصال ، گرانول با مواد اولیه زره پوش ، دیافراگم ، آسیاب برای آسیاب خام ، چکش برای آسیاب با رعد و برق سریع سر ، رگ فشار و ساختار هواپیما همچنين برای تولید قطعات صنعتی از قبیل چرخ های جرثقیل که در معرض ساییدگی ساینده هستند استفاده می شود.
اما در شرایط کارسخت، مقاومت اين فولاد نسبت به سایش بعد از مدتی کاهش می یابد. با افزایش ساییدگی سایز و ابعاد قطعات کاهش می یابد و برای اصلاح سطح نیاز به تعمیر مي باشد. در این راستا، برای استفاده مجدد از فولادMO40 (بلوک فولادی MO40) ، از روکشهای سخت روی سطح سخت استفاده می شود. استفاده مجدد از فولاد به تجزیه و تحلیل سطح، سختی و لایه های فولاد مي پردازد. روکش ها بر روي دو روش جوشکاری انجام می شود:
- میله های UP6-GF-50 شماره استاندارد 307 کاوش جوش
- UP6-GF-50-C. شماره استاندارد 420 کاوش جوش
مقاومت در برابر سایش در روکشهای ۳۰۷ و ۴۲۰ تولید شده توسط فشار مضاعف بیشتر از پوششهای تولید شده توسط تك فشارها است. بر اساس میکروگرافی های میکروسکوپ الکترونی، مکانیسم سایش نمونه ها با سختی بالا بسيار كمتر از ساير نمونه هاست.
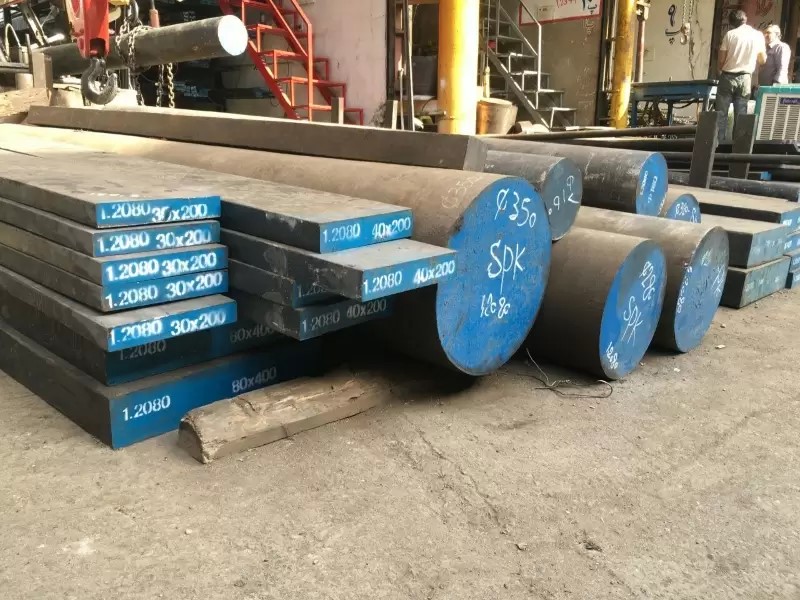
آرتا استیل تهران
آرتا استیل تهران متخصص واردات و توزیع انواع ورق های آلیاژی، استنلس استیل و فولاد ضدزنگ، میلگردهای استنلس استیل، لوله و پروفیل و ورقهای فنری، آمادگی خود را جهت همکاری و تأمین کلیه مقاطع فولادی و استنلس استیل به صنعتگران محترم اعلام می دارد. همچنین شما به راحتی می توانید با کارشناسان ما تماس و نسبت به ثبت سفارش خود اقدام نمایید .
دسترسی سریع به محصولات
میلگرد استیل | لوله استیل | استیل ضدزنگ | ورق نسوز | استیل ۳۰۴
ما را در شبکههای اجتماعی دنبال کنید
صفحه فیسبوک | صفحه اینستاگرام | لینکدین | مایاسپیس | پینترست | یوتیوب | ویکیپدیا |