انواع کوره ی تولید آهن
انواع کوره ی تولید آهن ؛ از فرآیند اصلی تولید آهن آلات مدرن به حساب میآید. خصوصیات مواد و کیفیت محصول نهایی توسط این کوره ها تعیین میشود. عرضه کالاهای با کیفیت در بازار به عملیات گرمایشی و سرمایشی در طی فرآیند تولید وابسته است. انواع کوره در مراحل مختلف تولید محصولات آهنی و غیرآهنی مثل ذوب قراضه، پیش گرمایش میله، عملیات حرارتی فولاد و شکل دهی گرم صفحات فلزی کاربرد دارد. در این مقاله به معرفی انواع کورههای مصرفی در صنعت و بررسی مزایا و معایب هر کدام میپردازیم.
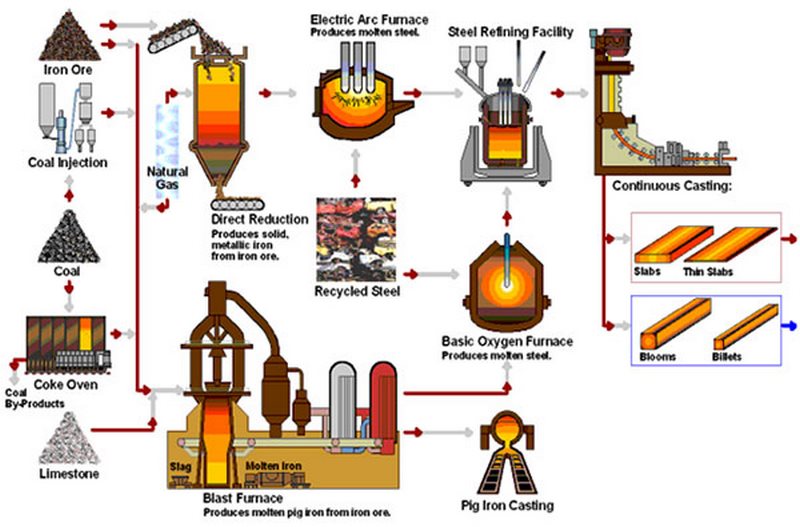
انواع کوره ی تولید آهن ، کوره بوته ای
یکی از قدیمی ترین و ساده ترین انواع کوره که در واحد ریخته گری مورد استفاده قرار میگیرد، کوره بوته ای است. هرچند که گذشت زمان و پیشرفت تکنولوژی باعث شده تا توجه به کوره بوته ای کمتر شود، اما همچنان درشرایط خاص، کوره بوته ای مورد استفاده قرار میگیرد. در این نوع کوره شارژ(ماده اولیه ) و سوخت با هم تماسی ندارد و حرارت از طریق هدایت مواد درون کوره را ذوب میکند. مواد نسوز مختلفی که در ساخت بوته به کار میرود باعث شده تا انواع کوره بوتهای کاربردهای متفاوتی داشته باشند. بوته گرافیتی، سیلیکون کاربایدی و شاموتی از رایج ترین بوته ها هستند.
بوته گرافیتی
بوتههای گرافیتی یکی از انواع بوتههای پرمصرف در ذوب فلزات هستند. کاربرد این نوع از بوته به علت حفظ ساختار تا دمای خیلی بالا (حدود ۳۵۰۰ درجه سانتیگراد)، هدایت حرارتی عالی و عدم واکنشدهی شیمایی با مذاب درونیاش گسترده است. بوته گرافیتی در دو نوع کوره القایی و بوتهای و به صورت افقی یا عمودی به کار میرود. ذوب آلومینیوم، مس و انواع آلیاژهایش چون برنج، فلزات نادر خاکی و گرانبها همانند نقره و طلا در این نوع از بوته انجام میپذیرد.
بوته گرافیتی نسبت به اکسیدشدن حساس است. لذا در محیط درزبندیشده برای جلوگیری از نفوذ اکسیژن و یا محیط کنترلشده با گاز خنثی، ار آن استفاده میشود. هدایت حرارتی عالی و امکان استفاده بهینه از انرژی حرارتی، استحکام شکست بالا و مقاومت نسبت به ضربه، مقاومت به اکسیداسیون و واکنشدهی با فلاکس مذاب و ساختار هموژن برای حفظ ساختار بوته تا دماهای خیلی بالا از عمده مزیتهای بوته گرافیتی میباشد.
سیلیکون کاربایدی
بوتههایی از جنس سیلیکون کارباید، در دو کاربرد ذوب فلز و نگهداری مذاب بکار میروند. مراحل نصب ومصرف این بوتهها کمی سخت و دارای چندین مرحله است. در ادامه به بیان آن به اختصار میپردازیم.
- محیط عملیاتی باید عاری از رطوبت باشد و حین جابجایی روکش درونی و بیرونی بوته آسیب نبیند.
- نصب بوته در مرکزیت کوره و تعبیه فضای آزاد در اطراف آن به جهت پیشبینی انبساط ان حین مذاب نمودن.
- شعله مشعل نباید در تماس با بدنه و کف بوته سیلیکون کاربایدی قرار گیرد.
- عملیات پخت برای بوته در دو کاربرد ذوب نمودن و حمل مذاب انجام گیرد.
در کاربرد ذوبسازی ، به مدت دو ساعت در دمای ۲۰۰ درجه سانتیگراد به بوته حرارتدهی میشود. تا رطوبت جذب و حذف گردد. سپس با حداکثر توان مشعل، دمای بوته به ۹۵۰ میرسد. حرارت دهی و شارژ قراضه فلزی در مراحل بعدی و پیوسته صورت میپذیرد. در کاربرد نگهداری مذاب، عملیات افزایش دما بوته تا ۹۵۰ درجه سانتیگراد مشابه بالاست. اما به مدت یک ساعت نیز در دمای ۹۵۰ درجه ثابت نگهداشته میشود. در موارد استفاده با فاصله زمانی کم، حرارت دهی تا ۲۰۰ درجه و برای دو ساعت قابل حذف است.
شاموتی
نامگذاری بوته شاموتی به کاربرد آجرهای شاموتی در ساختار آن برمیگردد. آجرهای شاموتی از جنس اکسید سیلسیوم یا آلومینیوم میباشند.کاربرد این آجرها در مصارف دمای بالایی چون دیواره داخلی کورهها، دستگاه دمش کوره بلند، ریختهگری فولاد، کورههای پخت کوره، صنعت شیشه، ذوب فلزات غیرآهنی و… نیز هست.
برای ذوب آلیاژ های با نقطه ذوب پایین و آلیاژ هایی مثل منیزیم که میل ترکیبی زیادی با اکسیژن دارند از بوته فولادی استفاده میشود. سوخت کوره بوته ای با مصرف گازوئیل، مازوت، گاز طبیعی و الکتریسیته تامین میشود. انواع کوره بوته ای بر حسب نوع ساختمان به صورت کوره ثابت ، ثابت با بوته متحرک یا گردان تولید میشود.
مزایا و معایب انواع کوره بوته ای
سادگی و سهولت ساخت، ارزانی و کیفیت مذاب خوب از جمله مزیت های کوره بوته ای است که سبب شده همچنان در کارگاه های کوچک استفاده از کوره بوته ای دراولویت باشد. اما این نکته را نباید از یاد برد که تلفات حرارتی در این نوع کوره ها بالا است.
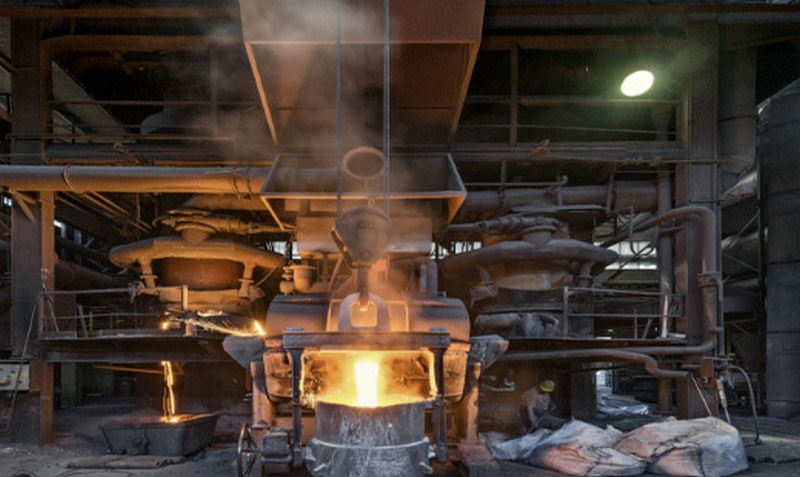
انواع کوره ی تولید آهن ، کورههای شعلهای
کوره شعلهای، تشعشعی یا روباده نیز نخستین بار در قرون وسطی برای ذوب برنز به منظور ریخته گری زنگ های کلیسا مورد استفاده قرار میگرفت. مواد شارژ در این کوره در تماس مستقیم با محصولات احتراق قرار گرفته و ذوب میشود. شارژ به دو طریق داخل کوره میشود: درب و سقف کوره.
سوخت مصرفی کوره شعله ای گازوئیل یا گاز طبیعی است. ظرفیت کوره تشعشعی برای ذوب آلیاژ های غیر آهنی از ۱۵تا۷۵ تن متغیر است، اما کوره های ۵۰۰ کیلوگرمی هم ساخته شده است. اگرچه این کوره ها به عنوان نگهدارنده تا ۹۰ تن نیز ظرفیت دارند. انواع کوره شعله ای درحالت ساکن به شکل مکعب مستطیل و استوانهای ساخته میشود. کوره تشعشعی در حالت گردان برای چدن ریزی مورد استفاده قرار میگیرد.
مزایا و معایب انواع کوره شعله ای
کوره شعله ای با ساخت ساده، حجم و سرعت بالایی در ذوب دارد و سرمایه گذاری زیادی احتیاج ندارد. به دلیل اینکه درجه حرارت مذاب چندان بالا نمی رود، راندمان کوره ها پایین (حدود ۲۰ تا ۳۰ درصد) است.
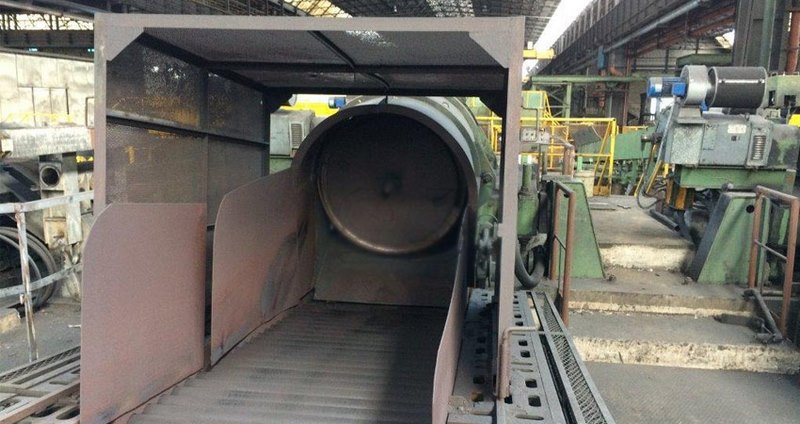
انواع کوره ی تولید آهن ، کوره کوپلا
متداول ترین روش ذوب چدن، استفاده از کوره کوپلا است. ساختمان کوره، استوانهای فولادی با پوشش جداره نسوز است. که قطر آن متناسب با ظرفیت و سرعت ذوب تغییر میکند. بخش های جانبی کوره کوپلا شامل پیش گرم کن هوا، ریل شارژ و محل تصفیه گاز های خروجی میشود. در این نوع کوره شعله در تماس مستقیم با شارژ ظرفیت ذوب از ۱۰۰ تا ده ها تن را دارد. بر اساس نوع و نحوه مصرف سوخت انواع کوره کوپلا در صنعت مورد استفاده قرار میگیرد.
مکانیزم دمش سرد
در این نوع کوره پیش از ورود شار کک با هوا میسوزد و به حالت التهاب در میآید. پس از رسیدن بلندی کک بستر به حد نصاب، مواد گدازنده یکباره یا متناوب بر روی آهن و کک اضافه شده و هوا جریان مییابد. به دلیل کم بودن عمر لایه نسوزاز دو کوره دمش سرد کنار هم استفاده میشود.
مکانیزم دمش گرم
کوره دمش گرم مشابه دمش سرد است با این تفاوت که برای پیش گرم کردن هوای ورودی کوره از گاز خروجی کوره استفاده میشود. با این عمل مصرف کک کاهش مییابد. لایه نسوز کوره دمش گرم، در مقابل دمش سرد عمر بیشتری دارد. سوخت مصرفی برخی از کورههای کوپلا گاز و گازوئیل است که به دلیل عدم مصرف کک آلودگی کمتری تولید میکنند.
مزایا و معایب انواع کوره کوپلا
نحوه کار با کوره کوپلا ساده است. با استفاده از آن حجم مذاب بالا حاصل می گردد. کوره های دمش سرد و دمش گرم به دلیل مصرف کک آلودگی تولید می کنند. کورههای کوپلا در رسیدن به فوق گداز های بالا انعطاف پذیری کمی دارند.
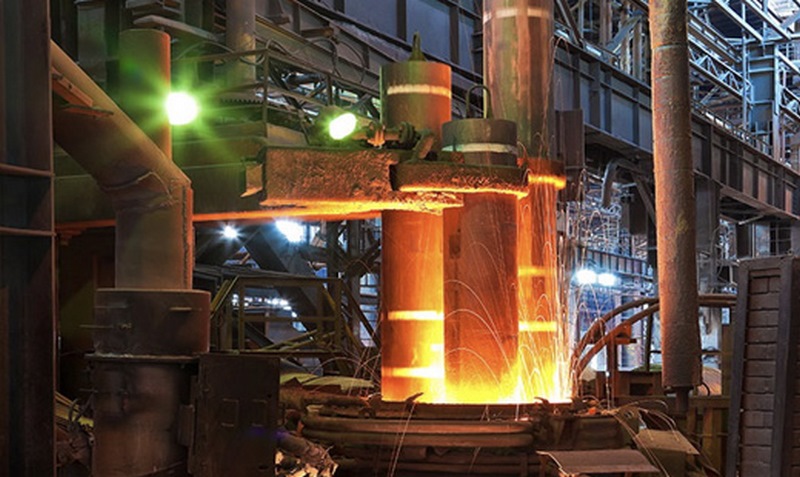
انواع کوره ی تولید آهن ، کوره مقاومتی الکتریکی
در کوره های مقاومتی حرارت لازم برای ذوب شارژ از طریق عبور جریان الکتریکی از المنتها تامین میشود. کوره های مقاومتی برای عملیلات حرارتی، پیش گرم کردن برای شکل دهی با فشار و ذوب فلزات کاربرد دارند. المنتها از آلیاژ های با نقطه ذوب بالا و مقاوم به خوردگی و اکسیداسیون ساخته شدهاند. جریان الکتریکی با شدت بالا از المنت عبور کرده و تحت یک سیستم کنترل کننده با قطع و وصل جریان برق حرارت تولیدی کنترل میشود.انواع کوره مقاومتی در دو نوع کوره مقاومتی با گرم کننده مستقیم و کوره مقاومتی با گرم کننده غیر مستقیم موجود است.
اگر جریان برق با ولتاژ کم و جریان زیاد از خود شارژ عبور کند به آن کوره مقاومتی با گرم کننده مستقیم میگویند. این کوره بیشتر برای گرم نگه داشتن و ذوب کاربرد دارد. در کوره های مقاومتی با گرم کننده غیر مستقیم جریان برق از المنت های فنری که دور کوره پیچیده شده است میگذرد و حرارت ابتدا به بوته و سپس از بوته به شارژ منتقل میشود.
مزایا و معایب انواع کوره مقاومتی الکتریکی
در این روش می توان ترکیب شیمیایی مذاب را کنترل کرد. بزرگترین عیب این روش علاوه بر زیاد بودن هزینه ها به دلیل استفاده از الکتریسته، ظرفیت کم این کوره ها ( حداکثر ۵۰۰کیلو گرم) است.
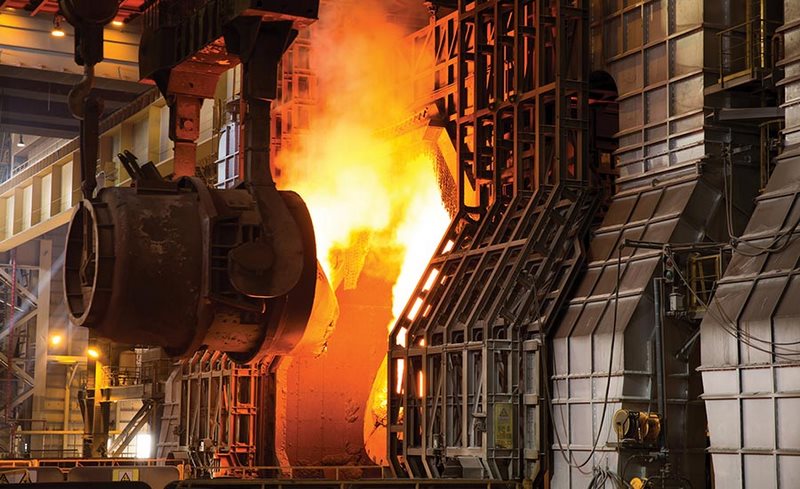
انواع کوره ی تولید آهن ، کوره القایی
در کوره القایی که جزء کوره های مدرن محسوب میشود، فلز هادی مثل چدن درون سیم پیچ یا کویل قرار میگیرد. میدان مغناطیسی که در اثر عبور جریان الکتریکی از سیم پیچ در وسط سیم پیچ ایجاد میشود باعث ایجاد جریان های گردابی در فلز شده و آن راذوب میکند. انواع کوره القایی بر حسب فرکانس به سه دسته فرکانس پایین ۵۰هرتز، فرکانس متوسط ۲۰۰تا ۱۰۰۰۰ هرتز، فرکانس بالا ۱۰۰۰۰هرتز به بالا تقسیم میشود. کوره های فرکانس پایین راندمان پایینی دارند و بیشتر به عنوان کوره های نگهدارنده کاربرد دارند و برای ذوب توصیه نمیشود. کوره های فرکانس بالا غالبا برای ذوب در آزمایشگاه ها استفاده می شوند. از کوره ذوب القایی، برای تهیه مذاب فولاد از قراضه و آهن اسفنحی استفاده میشود. از این مذاب ، برای ریخته گری انواع مقاطع فولادی از جمله میلگرد، تیرآهن و … را تولید کرد.
مزایا و معایب انواع کوره القایی
از مجموعه مزیت های کوره القایی میتوان به کنترل ترکیب شیمیایی، توزیع حرارت مطلوب، عدم محدودیت افزایش دما و مصرف انرژی کمتر نسبت به کوره مقاومتی اشاره کرد. قراضه و شارژ مصرفی این روش باید تمیز باشند، چرا که به به دلیل وجود تلاطم و سرد بودن مذاب در سطح فوقانی امکان تصفیه مذاب وجود ندارد. استفاده از الکتریسیته باعث افزایش هزینه نهایی میشود.
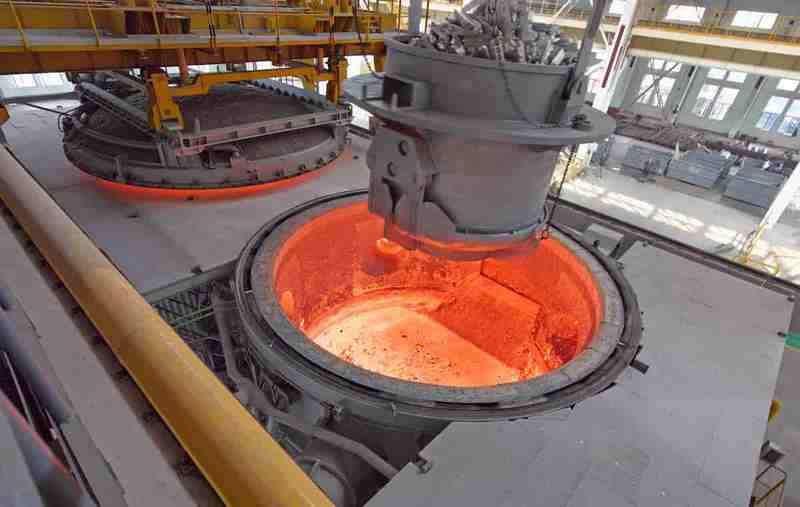
انواع کوره ی تولید آهن ، کوره قوس الکتریکی
ساختمان این کوره ها یک حمام بزرگ با بدنه فولادی با پوشش ماده نسوز است. به دلیل بالا بودن دمای بدنه که باعث از بین رفتن ماده نسوز میشود، سقف و بدنه با لوله های آبگرد پوشیده شده است. تفاوت انواع کوره قوس به نحوه ایجاد قوس مربوط است.
ماده شارژ از طریق قوس موجودبین الکترود ها یا با ایجاد قوس بین الکترود و شارژ ذوب میشود. به اولین روش قوس الکتریکی غیر مستقیم به دومی قوس الکتریکی مستقیم می گویند. قوس مستقیم در ذوب فولاد و چدن و قوس غیر مستقیم برای ذوب آلیاژ های مس کاربرد دارد.
مزایا و معایب انواع کوره قوس الکتریکی
در کوره قوس می توان از قراضه های ارزان استفاده کرد و تمیز بودن آن الزامی نیست. مزیت مهم این کوره ها امکان تصفیه مذاب است. دمای قوس از کوره القایی بیشتر است. هزینه انرژی برای کوره القایی از کوره قوس کمتر است. اما هزینه گرافیت و نسوز مورد استفاده در کوره قوس باعث افزایش هزینه های عملیاتی میشود.
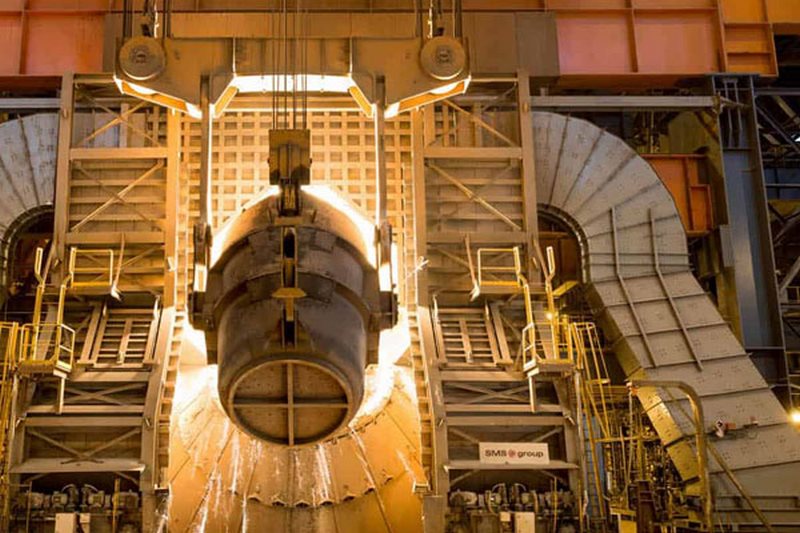
آرتا استیل تهران متخصص واردات و توزیع انواع ورق های آلیاژی، استنلس استیل و فولاد ضد زنگ، میلگردهای استنلس استیل، لوله و پروفیل و ورقهای فنری، آمادگی خود را جهت همکاری و تأمین کلیه مقاطع فولادی و استنلس استیل به صنعتگران محترم اعلام می دارد. همچنین شما به راحتی می توانید با کارشناسان ما تماس و نسبت به ثبت سفارش خود اقدام نمایید .
دسترسی سریع به محصولات
میلگرد استیل | لوله استیل | استیل ضد زنگ | ورق نسوز | استیل ۳۰۴