شکل دهی فلزات صنعتی
شکل دهی فلزات صنعتی عملیاتی که در طی آن فلز به شکل و ساختار جدیدمی رسد. که دارای خواص و ویژگیهای خاصی است. شکل دهی فلزات به دو روش کلی انجام میشود. روش اول تغییر شکل در فرایندهای ورقکاری و روش دوم تغییر شکل در توده فلز یا شکلدهی حجمی است. به طور مثال اسلب و شمش با استفاده از این روش به دیگر مقاطع فولادی تبدیل میشود. ورق، لوله، تیرآهن، میلگرد، نبشی، ناودانی و پروفیل، از اصلیترین این محصولات است که کاربرد بسیار گستردهای در صنایع مختلف دارند.
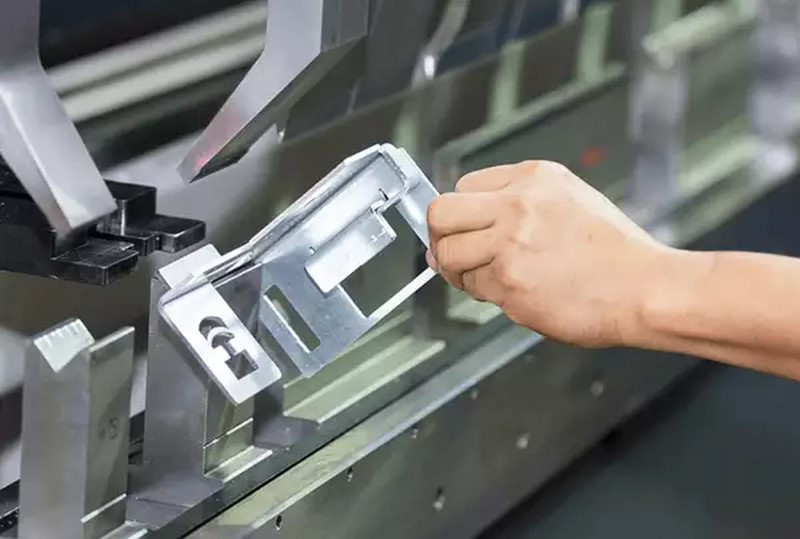
لزوم انجام فرایندهای شکل دهی فلزات صنعتی
شکل دهی فلزات صنعتی ؛ بهطورکلی پس از استخراج آهن و فولادسازی در کورههای کنورتور، مذاب فولاد آماده تبدیل به محصولات متنوع فولادی است. ریختهگری فولاد به دو صورت شکلریزی و شمشریزی انجام میشود. در ریختهگری شکل ریزی، محصول معمولاً هندسه پیچیدهای دارد، به همین دلیل در قالبهای مخصوص، بهصورت شکل نهایی ریختهگری میشود. فرایند شکل دهی فلزات به کمک ماشینکاری نهایی میشود و قطعه بهدقت ابعادی موردنظر میرسد. جهت دستیابی به خواص مکانیکی ایدهآل، یک مرحله عملیات حرارتی روی قطعه انجام میشود.
با استفاده از روش شمشریزی ، مذاب فولاد به شکل یکی از مقاطع بیلت، بلوم یا اسلب (تختال) تبدیل میشود. مقطع این محصولات بهصورت مربع یا مستطیل است و در ابعاد با یکدیگر تفاوت دارند. با استفاده از روش شمشریزی، مذاب فولاد به شکل یکی از مقاطع بیلت، بلوم یا اسلب (تختال) ریخته میشود. مقطع این محصولات بهصورت مربع یا مستطیل است و در ابعاد با یکدیگر تفاوت دارند. از بیلت برای ریختهگری تولید میلگرد آجدار و ساده و مقاطعی مثل نبشی، ناودانی، سپری و … استفاده میشود.
همچنین از مقطع بلوم که ابعاد بزرگتری نسبت به بیلت دارد، برای تولید لوله مانیسمان استفاده میشود. بیشترین استفاده تختال در تولید ورق است. برای تولید این مقاطع از انواع روشهای شکلدادن فلزات استفاده میشود.
مهمترین این فرایندها نورد است که بیشترین کاربرد را در ساخت این مقاطع دارد. از دیگر فرایندهای شکل دهی فلزات میتوان به فورج، کشش، پرس اشاره کرد.
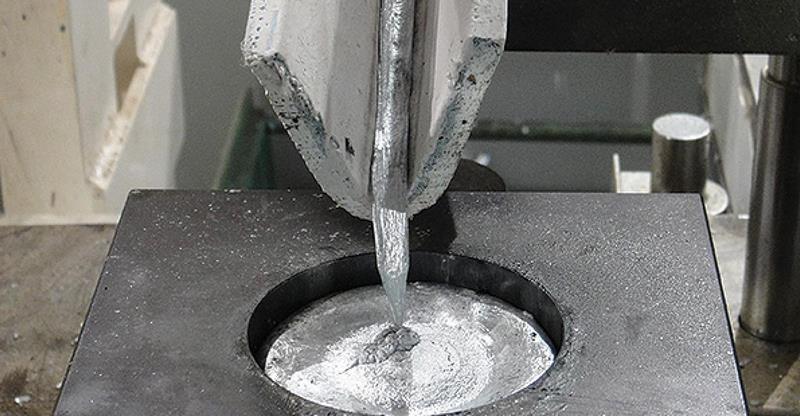
روش های شکل دهی فلزات
از روش های شکل دهی فلزات میتوان به چند مورد اشاره کرد که در ادامه روشها و اصول شکل دهی فلزات را بررسی میکنیم:
کشش سیم
یکی از روش های شکل دهی فلزات در متالوژی، کشش سیم است. عملیات کشش به فرایندی اطلاق میگردد که طی آن، فلز از درون قالب بهوسیله نیروی کششی، خارج شود. بیشتر سیلان فلز درون قالب، توسط نیروی فشاری ناشی از اثر متقابل قالب و قطعه کار حاصل میشود. معمولاً قطعات با تقارن محوری توسط فرایند کشش تغییر شکل مییابند. به فرایند کاهش قطر سیم، میله باریک فلزی یا مفتول توپر در اثر کشش، کشش سیم، میله و یا مفتول اطلاق می گردد.
به سیمهای تهیه شده از طریق روش نورد، اصطلاحاً مفتول می گویند. مفتول مادة اولیه برای تولید سیمی است که قطر آن کمتر از یکسانتی متر باشد. عملیات کشش معمولاً در حالت سرد انجام میشود. اگرچه در مواردی که میزان تغییر شکل زیاد باشد بهصورت گرم نیز صورت میگیرد.
کشش تسمه
تسمه یکی از محصولات نورد تخت است که پهنایی کمتر از ۶۱۰ میلی متر و ضخامت بین ۰.۱۳ تا ۴.۷۶ میلی متر دارد. تسمه ها پس از نورد داغ، عملیات آنیل و سپس اسیدشویی، نورد سرد میشوند. با توجه به میزان ضخامت درخواستی، نورد سرد در چند مرحله انجام میشود. هرگاه یک تسمهی فلزی با پهنای w۰ و ضخامت اولیهی h۰ از میان یک قالب گوهای شکل با شیب یکسان به سوی خط مرکزی کشش یابد ، به این فرایند کشش تسمه اطلاق میشود. کشش تسمه از روشهای متداول شکل دهی فلزات نیست. پیرامون این موضوع در مکانیک نظری فلز کاری درباره آن مطالعات زیادی انجام گردیده است. از آنجا که w۰ خیلی بزرگتر از t۰ ست، لذا در حین کشش حالت کرنش صفحهای به وجود میآید و پهنای تسمه تغییر نمیکند.
کشش لوله
لولهها و یا استوانههای توخالی که توسط فرایندهای شکل دهی؛ مانند اکستروژن و نورد تولید میشوند، معمولاً توسط فرایند کشیدن، به شکل نهایی درآمده و پرداخت سطحی میشوند. اگرچه هدف اصلی از این فرایند کاهش قطر و ضخامت لوله است، ولی در موارد نادری افزایش ضخامت نیز ایجاد میشود. بهطورکلی میتوان فرایند کشش لوله را به چهار دسته کشش لوله بدون توپی، کشش لوله توسط سمبه، کشش لوله توسط توپی ثابت و کشش لوله توسط توپی شناور تقسیمبندی کرد.
در کلیة این روشها یک انتهای لوله، با پرسکاری توسط دو فک نیمگرد باریک میشود و این انتهای باریک شده از قالب کشش عبور داده و توسط ابزاری که روی کالسکه دستگاه بسته شده، محکم گرفته میشود. سپس کالسکة کشش، لوله را از داخل قالب بیرون میکشد.
خم کاری
خم کاری فرایندی است که طی آن، به ورقهای تخت فلزی شکل و زاویه داده میشوند و بدون شکست و یا نازک شدن به شکل موردنظر درمیآیند. از جمله کاربردهای این فرایند، میتوان به تولید ناودانی و نبشی پرسی اشاره کرد. شکل دهی فلزات از نوع ورق در صنعت قطعهسازی از اهمیت بسیار زیادی برخوردار است. بسیاری از قطعات مصرفی از سینیهای غذاخوری تا پنلهای جداسازی دیوارهای صنعتی به کمک روش شکل دهی فلزات تولید میشوند.
آهنگری یا فورجینگ
فورجینگ یکی از روش های شکل دهی فلزات است که بهمنظور تبدیل فلز به شکلی دیگر توسط پتککاری و یا پرسکاری انجام میشود. آهنگری از قدیمیترین هنرهای فلزکاری محسوب میشود و منشأ آن به زمانهای بسیار دور بر میگردد. در حقیقت در چندین هزار سال پیش فلزاتی مانند نقره و طلا بدون استفاده از قالب، آهنگری (آهنگری باز) میشدند. اما از ۲۰۰۰ سال پیش، استفاده از قالب جهت آهنگری قطعات مرسوم گردید. ایجاد ماشینآلات و جایگزینی آن با بازوی آهنگر، از دوران انقلاب صنعتی آغاز گردید. امروزه ماشینآلات و تجهیزات آهنگری متنوعی وجود دارند که به کمک آنها میتوان به ساخت قطعات کوچکی بهاندازه یکمهره تا قطعات بزرگی مانند روتور توربین و قطعات کشتی و خودرو اشاره کرد.
اتوکشی
اتوکاری نیز یکی از روش های شکل دهی فلزات محسوب میشود که برای از بین بردن اعوجاج و ناهمواریهای سطح ورق مورد استفاده قرار میگیرد.
شکل دهی چرخشی
در این روش شکل دهی فلزات، ابزار شکلدهی بهصورت چرخشی کار میکنند و باعث تغییر شکل فلز میشوند. این روش برای تولید وسایلی از جمله قابلمه، قوطی و ظروف دیگر کاربرد دارد.
کشش عمیق
از جمله روش های شکل دهی فلزات کشش عمیق می باشد. کشش عمیق یکی از انواع روشهای شکلدهی ورقهای مسطح و تبدیل آنها به محصولات فنجانی شکل است که از آن جمله میتوان به وان حمام، سینک ظرفشویی، لیوان، محفظههای پوستهای و گلگیر خودرو به کار اشاره کرد.
اکستروژن
شکل دهی فلزات به روش اکستروژن یکی از جدیدترین روشها محسوب میشود. بهطوریکه اولین فرایند، مربوط به اکستروژن لولههای سربی در اوایل قرن نوزدهم است. این فرایند به این شکل عمل میکند که ماده خام درون قالب قرار میگیرد و به شکلی مطابق با سطح مقطع سوراخ خروجی دستگاه قالب درمیآید. بهطورکلی اکستروژن، برای تولید اشکال با سطح مقطع نامنظم به کار گرفته میشود، اگرچه میلههای استوانهای و یا لولههای توخالی از جنس فلزات نرم میتوانند با استفاده از این فرایند تغییر شکل یابند. امروزه اکستروژن فلزات و آلیاژهایی مانند آلومینیوم، روی، فولاد و آلیاژهای پایة نیکل میسر است. فرایند اکستروژن، بسته به تجهیزات مورداستفاده، به دودستة اصلی اکستروژن مستقیم و اکستروژن غیرمستقیم تقسیمبندی میشوند.
کشش سیم یا روزن رانی
این روش شبیه روش اکستروژن است، اما تفاوتی کمی نیز دارد. در این روش قطعهای که قابل شکل دهی است از طریق دهانه قالب کشیده تا سطح مقطع قالب را بگیرد.
نورد
نورد به فرایند شکلدهی فشاری گفته میشود که تغییر شکل فلز از طریق عبور آن از بین غلتکها صورت میگیرد. امروزه استفاده از غلتک، یکی از متداولترین روشهای شکل دهی فلزات محسوب میشود. از امتیازهای این روش ظرفیت تولید بالای آن است. بهطوریکه میتوان روزانه چند صد تن فلز را نورد کرد. محصول نورد ممکن است فرآوردة پایانی و یا مراحلی از شکل دهی فلزات باشد. از جمله محصولات نورد میتوان به ورق، میلگرد ساده، میلگرد آجدار، تیرآهن، هاش، سپری، نبشی فابریک و ناودانی فابریک اشاره کرد. دستهبندی فرایندهای نورد میتواند بر اساس دستگاهی که شکل دهی فلزات در نظر گرفته شده است، بهصورت نورد و یا دمای نورد باشد. از لحاظ دمای کاری، نورد به دو دستة نورد سرد و نورد گرم تقسیم میشود.
نورد سرد
نورد سرد معمولاً برای تولید ورق و تسمه با پرداخت سطحی و دقت ابعادی بالا به کار گرفته میشود. همچنین نورد سرد یکی از روش های شکل دهی فلزات است که بهمنظور استحکامبخشی فلز انجام میشود. مهمترین کاربردهای محصولات نورد سرد در اتومبیل، تجهیزات خانگی مانند یخچال، اجاقگاز، ماشینهای ظرفشویی و لباسشویی، دستگاههای الکتریکی، مخازن و تجهیزات و مصالح ساختمانی است. ورقهای تولید شده توسط نورد سرد، ابتدا تا حداقل ضخامت ممکن (حدود ۱/۵ میلیمتر) از طریق نورد گرم تولید شده، سپس بعد از اسیدشویی، کاهش ضخامت و در مواردی، تغییر شکل آنها توسط فرایند نورد سرد انجام میپذیرد.
علاوه بر کاهش ضخامت و رساندن قطعه بهدقت ابعادی موردنظر، حذف نقطة تسلیم از ورقهای فولادی، از دیگر کاربردهای نورد سرد است. در حقیقت چون وجود نقطة تسلیم، باعث بهوجودآمدن شرایط تغییر شکل ناهمگن در روش های شکل دهی فلزات (بهویژه کشش عمیق) میشود، بنابراین حذف آن از اهمیت به سزایی برخوردار است. انجام یک مقدار کار مکانیکی نورد که اصطلاحاً به نورد بازپخت (آنیل) معروف است، باعث حذف نقطة تسلیم میشود. صافکردن ورقهای نورد شده نیز، از دیگر کاربردهای نورد سرد است، بهطوریکه با استفاده از فرایند نورد، ترازکردن غلتکی (که شامل دودسته غلتک با قطرکم است) انحنای ناشی از فرایندهای قبلی برطرف میشود.
در حقیقت در این فرایند، دودسته غلتک با قطرکم، به نحوی قرار گرفتهاند که ردیفهای بالایی و پایینی نسبت به هم انحراف دارند. وقتی ورق داخل ترازگر میشود، بهطرف بالا و پایین تغییر شکل پیدا کرده و با بیرون آمدن از غلتکها صاف میشود.
نوردگرم
شکل دهی فلزات به روش نورد، اولین عمل کارگرم است که اهمیت بسیار بالایی دارد. دستگاهی که شکلدادن فلزات به روش نورد گرم را انجام میدهد، از دو غلتک دوجهته به قطر بیش از ۶۰ تا ۱۴۰ سانتیمتر تشکیل شده است. مهمترین نکتهای که فرایند نورد گرم را از نورد سرد متمایز میسازد، دمای آن است. در حقیقت نورد کردن قطعه در دمایی بالاتر از دمای تبلور مجددش، نورد گرم نام دارد. ازآنجاکه در فرایند نوردگرم، فاصلة زمانی بین کار مکانیکی و فرایند تبلور مجدد بسیار کوتاه است، بنابراین قطعه همزمان تحتتأثیر کار سرد قرار میگیرد، بلافاصله تبلور مجدد نیز میشود.
از مهمترین مزایای نورد گرم میتوان به موارد زیر اشاره کرد:
- توانایی بسیار بالای ماده برای تغییر شکل، به دلیل افت تنش سیلان (مقدار تنش موردنیاز برای شکلپذیری فلز) ناشی از افزایش دما
- بازگشت ماده به ساختار میکروسکوپی اولیة خود بلافاصله پس از تغییر شکل
در مقابل این مزیتها، محدودیتهایی نیز وجود دارد، از جمله:
- اکسید شدن ناشی از درجه حرارت بالا
- حساسبودن شکلپذیری به درجه حرارت، بهویژه فولادها که در محدودة حرارتی ۲۵۰ تا ۳۵۰ درجه سانتیگراد دچار تردی آبی میشوند
- افزایش نقش ضریب اصطکاک
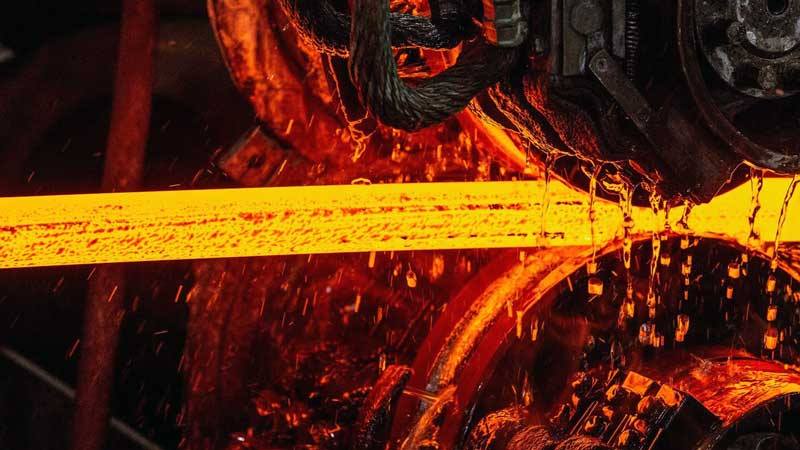
از لحاظ چینش غلتکهای نورد، این روش به چند دسته تقسیم میشود که در شماتیک زیر نشاندادهشده است، دلیل استفاده از چند غلتک پشتیبان، کاهش قطر غلتک کاری است. با کاهش قطر غلتک کاری، سطح تماس آن با ماده کاهش پیدا میکند، به همین دلیل اصطکاک فرایند کاهش مییابد. همچنین وجود غلتکهای پشتیبان مانع از خمیدگی غلتک کاری میگردد. این موضوع به بهبود دقت ابعادی محصول خروجی کمک میکند. تولید مقاطع نازک با روشهای چند غلتکه میسر است، همچنین در نوع سه غلتکه، نورد بهصورت رفت و برگشتی انجام میگردد، ورق از پایین وارد میشود و بعد از خمشدن، در مسیر بر عکس از بین دو غلتک بالایی خارج میگردد.
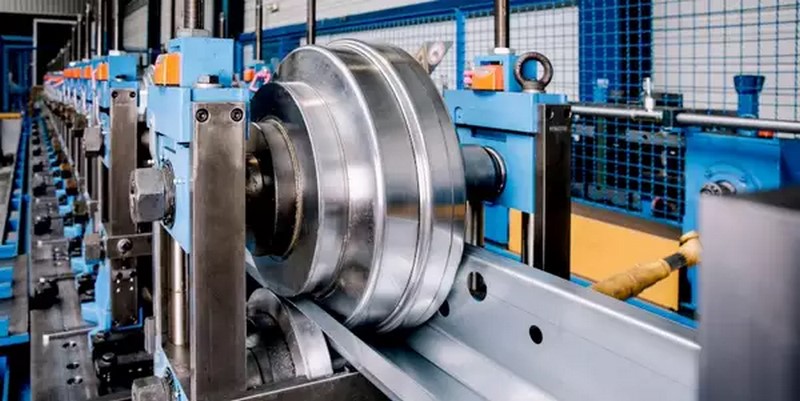
سخن پایانی
شکل دهی فلزات صنعتی از روشهای مهم در ساخت و تولید فلزات محسوب میشود. که بهصورت ورقکاری و شکلدهی حجمی صورت میگیرد. ورقکاری به چند مدل انجام میشود که از آن جمله میتوان به برشکاری، خمکاری و کشش عمیق و … اشاره کرد و شکلدهی حجمی شامل روشهای اکستروژن، آهنگری، نورد، کشش مفتولی و … میشود. در مورد هرکدام از این روشها بهاختصار توضیحاتی بیان شد. شکل دهی فلزات باعث تبدیل اسلب و شمش به مقاطع دیگر از جمله نبشی، میلگرد، ناودانی، تیرآهن و … میشود. مراحل طیشدن این فرایند در تولید محصول باکیفیت، بسیار اهمیت دارد.
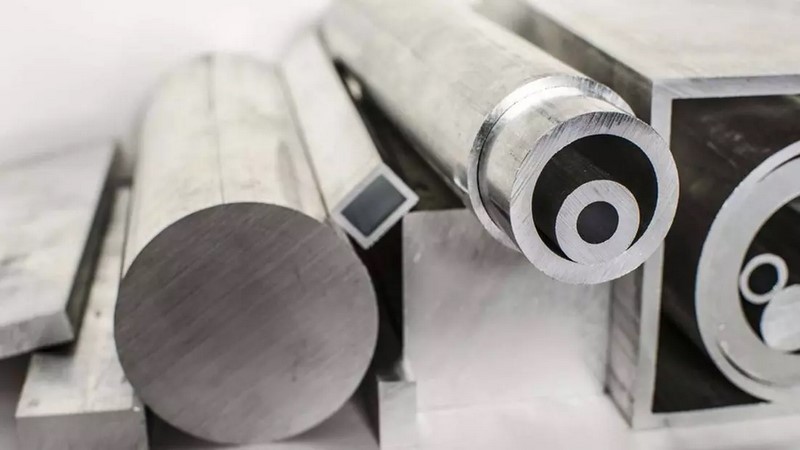
آرتا استیل تهران متخصص واردات و توزیع انواع ورق های آلیاژی، استنلس استیل و فولاد ضد زنگ، میلگردهای استنلس استیل، لوله و پروفیل و ورقهای فنری، آمادگی خود را جهت همکاری و تأمین کلیه مقاطع فولادی و استنلس استیل به صنعتگران محترم اعلام می دارد. همچنین شما به راحتی می توانید با کارشناسان ما تماس و نسبت به ثبت سفارش خود اقدام نمایید .
دسترسی سریع به محصولات
میلگرد استیل | لوله استیل | استیل ضد زنگ | ورق نسوز | استیل ۳۰۴